- Joined
- Aug 20, 2021
- Messages
- 10

The exhaust thread repair that was done by the previous owner of my 1973 850 Norton failed. An aluminum insert was installed in the head then welded in place. The weld failed and the insert pulled out, one side only, Hopefully, you can see the photos in the Imgur link below.
When I cleaned things up, I found the fit between the insert and the head to be very loose. The carbon deposits in that area on my initial disassembly indicates that. I would have thought to be a press fit.
Now where to go from here? I've contacted James Comstock, but I don’t believe his usual process of repair will apply here, that is, installing a brass insert. Can anyone suggest alternatives?
Included are photos of the cleaned up exhaust port showing how little material is left in that area.
Any help would be greatly appreciated.
Regards,
Ken Hiebert
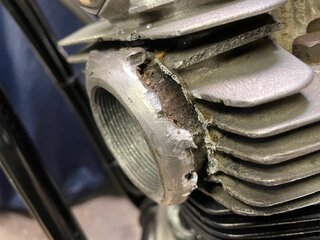
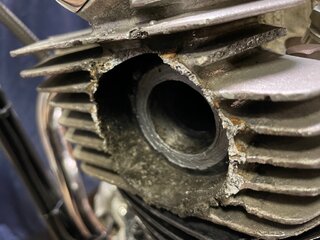
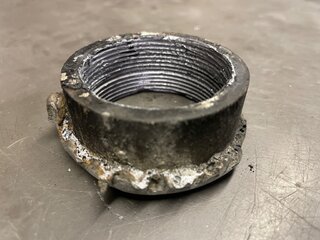
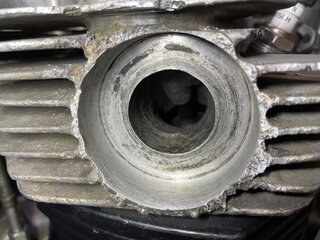
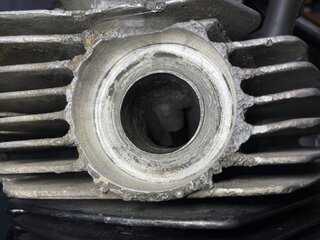
Right side, still intact:
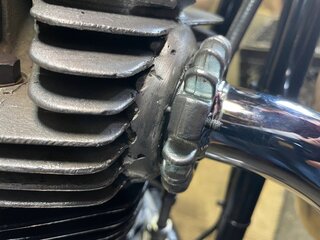
When I cleaned things up, I found the fit between the insert and the head to be very loose. The carbon deposits in that area on my initial disassembly indicates that. I would have thought to be a press fit.
Now where to go from here? I've contacted James Comstock, but I don’t believe his usual process of repair will apply here, that is, installing a brass insert. Can anyone suggest alternatives?
Included are photos of the cleaned up exhaust port showing how little material is left in that area.
Any help would be greatly appreciated.
Regards,
Ken Hiebert
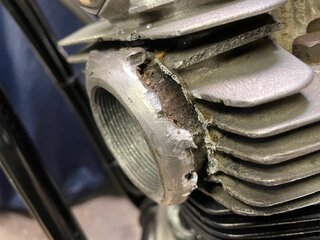
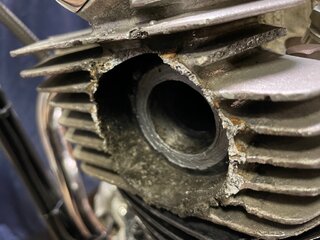
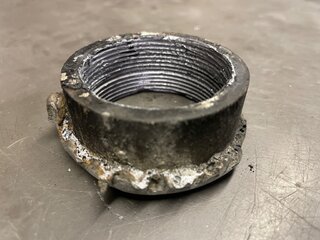
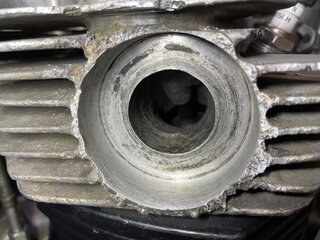
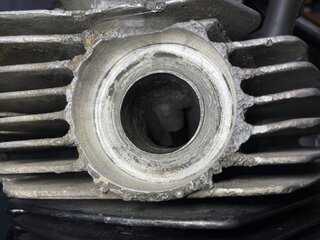
Right side, still intact:
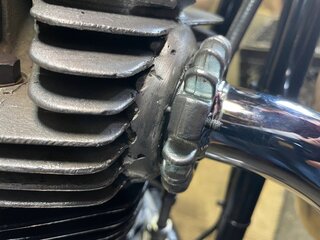
Last edited: